Continuous Improvement: SMED
- Jim Voigt
- Jun 17
- 4 min read
A common goal among many of us is improvement—whether in personal traits like knowledge, fitness, or health, or in mastering skills such as golf, trap shooting, or pickle-ball. In the workplace, our focus may shift to enhancing machine performance, processes, or production teams. No matter the context, the desire for continuous improvement drives us to always reach for the next level of performance. So, is there an organized way to pursue this in our work environment?
Numerous improvement philosophies and tools exist, but Lean/Six Sigma stands out for its proven track record. Originating at Motorola in the 1980s and further developed in Japan, Six Sigma focuses on eliminating defects and variability, while Lean principles trace back to Henry Ford, emphasizing process flow and waste reduction. Taiichi Ohno at Toyota created the Toyota Production System (TPS), which forms the foundation of modern Lean Principles. The combination of these methodologies offers an effective roadmap for achieving continuous improvement.
Remember: continuous improvement is a path, not a destination.
Among the valuable Lean tools for waste elimination, two that are easily applicable in our industry are Value Stream Mapping (VSM) and Single-Minute Exchange of Dies (SMED). VSM visualizes an entire process, enabling the analysis of inefficiencies and bottlenecks, while SMED concentrates on reducing the time required to switch between different production processes, thereby minimizing downtime and increasing efficiency.
Developed by Shigeo Shingo, a Japanese industrial engineer, SMED is integral to the Toyota Production System. The term "Single-Minute Exchange of Die" refers to the goal of reducing changeover times to under ten minutes. In its early days, Toyota faced fierce competition from the “big three” American car manufacturers but had limited presses for fabrication, which required frequent die changes that could take 90 minutes or more. By implementing the SMED process, Toyota reduced these changeovers to under ten minutes—some as low as five minutes—a remarkable 94% reduction.
SMED principles also shine in motorsport racing, particularly in NASCAR and Formula 1. Pit crews in both arenas utilize SMED to minimize the car's downtime in the pits and maximize track time. For example, NASCAR pit stops that once took several minutes now average around 12 seconds, with the record stop taking as little as 8 seconds.
So, how does SMED work? Changeovers consist of steps known as “elements,” divided into two types:
- Internal Elements: Tasks that must be performed while the equipment is stopped.
- External Elements: Tasks that can be completed while the equipment is still running.
The SMED process focuses on converting as many internal elements to external ones as possible and simplifying all elements. The SMED process comprises four basic steps:
1. Analyzing Current Processes: Identify and measure the time taken for set-ups or changeovers.
2. Separating Internal and External Setup: Distinguish between tasks that can be done while the equipment is running (external) and those that can only be performed when stopped (internal). Convert internal tasks to external where feasible.
3. Streamlining Processes: Improve or re-engineer internal setups for efficiency. This may include equipment modification, specific tool packages, and training. Eliminate any unnecessary steps.
4. Standardizing Procedures: Document improved setup processes to ensure consistency.
How can a tool developed for manufacturing like SMED be applied to the grain handling and processing industries? In my previous work with continuous improvement, I have two notable examples of applying SMED.
The first involved changing out rolls in a flour mill's roll stand. Before implementing SMED, roll changes took 7-8 hours or more. After beginning the SMED process, this time was reduced to 6 hours, then to 4 hours, and eventually to around 2 to 2.5 hours. One team even achieved a 90-minute changeover time. For facilities with multiple roll stands, this translates to significant increases in production capacity.
The second example pertains to date code changeovers in a refined packed oil facility. Prior to SMED, changing out date and lot numbers on the coders took 5 to 6 minutes. By applying the SMED process, this time was reduced to under one minute. While saving four minutes per change may seem minor, with four packaging lines performing 12 to 15 changes daily, the cumulative savings added up to 4 hours of additional production time per day.
What other areas might benefit from the SMED process? Any process with multiple steps that occurs frequently or has significant implications if not performed efficiently is a candidate. A few potential applications include:
- Tarping a ground pile
- Changing out a belt in a bucket elevator leg
- Jacking a grain bin
- Conducting physical grain inventories
- Loading vessels, barges, or trains
- Changeovers in feed mills or food plants
I encourage you to share your experiences or thoughts regarding other applications of SMED.
What barriers should you consider before implementing SMED? First, ensure there is a clear understanding of where productive time is being lost, and make decisions on improvement initiatives based on solid data. This requires a system for collecting and analyzing performance data. Additional barriers to consider include:
- Resistance to Change: Employees accustomed to existing methods may resist adopting new processes or practices.
- Initial Investment: Implementing SMED may require investments in training, tools, and process re-engineering.
- Skill Levels: Employees may need training to adapt to new methods or effectively use new tools.
- Cultural Factors: An organizational culture that does not prioritize continuous improvement can hinder SMED adoption.
It is crucial to note that the SMED process does not involve shortcutting critical safety protocols. Always operate equipment with guards in place and follow Lockout/Tagout (LOTO) or hot work procedures.
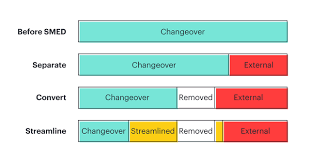
In summary, applying SMED principles across various processes in grain handling and processing can significantly enhance efficiency and reduce downtime. This approach plays a vital role in maintaining high grain quality, ensuring food safety, and sustainability of the business. By focusing on rapid changeovers, streamlined cleaning protocols, efficient operations, and traceability, participants in the grain, feed, and food supply chain can mitigate risks associated with lost time, higher operating costs, contamination, and uphold product integrity.
Thank you for taking the time to read this post! This is just one of many that will explore how Lean/Six Sigma continuous improvement tools can be applied in the grain industry. Your feedback fuels this blog, so don’t hesitate to share your thoughts or personal experiences. Together, we can cultivate a better understanding of modern grain handling and processing.
To learn more about SMED, visit: [SMED Overview](https://www.leanproduction.com/smed/).
Best wishes,
Grain Guy Fifty
Comentários